Evaluating and Repairing a Concrete Substrate
Author: Lee Polevoi | January 9, 2025
The quality of a concrete substrate, as part of overall waterproofing projects, is among a commercial waterproofer's top priorities. One area in critical need of waterproofing material is a building's concrete substrate. These substrates may be composed of precast concrete panels or poured as part of the on-site construction process. Not only does this fire-resistant substrate help ensure first-rate structural integrity, it also performs commendably in regions of extreme weather conditions and is one of the most commonly used construction materials.
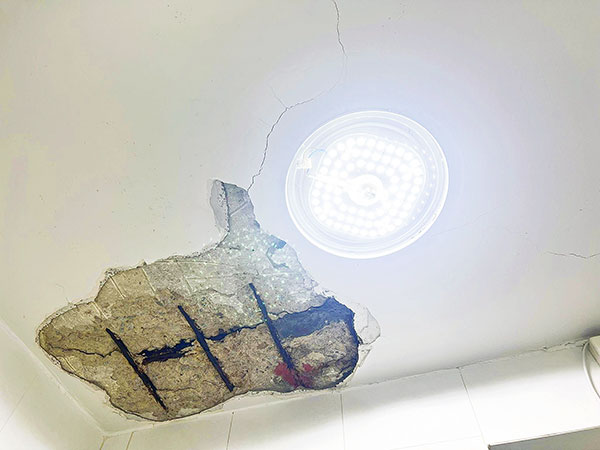
Maintaining the strength of concrete substrates is part of every commercial waterproofer's arsenal. Whether the project involves above grade or below grade waterproofing, applying coatings, sealants or sheet goods or restoring and repairing concrete, ensuring a sound substrate is key to a project's success.
Below-grade waterproofing material is applied to surfaces below ground level (such as foundations or tunnels) to keep water or moisture from seeping into a structure's lowest level. This helps decrease the risk of humidity and moisture creating unfavorable conditions for equipment and other structural elements.
Perhaps most importantly, a concrete substrate presents a major barrier to the threat of moisture infiltrating and eventually damaging a building's structure.
Damage Over Time
The quality of concrete substrates can deteriorate over time. One of the most common forms of concrete deterioration is corrosion, or rusting of the embedded steel reinforcement, (rebar). Over time, this rebar can start to rust, putting stress on the concrete substrate as this rust expands. It is important to evaluate the concrete substrate to determine if corrosion or other deterioration is present.
Visual Inspections of Danger Areas
Determining the soundness of concrete substrates starts with an expert's visual inspection of a commercial building's interior and exterior. A wide range of potential problems can be identified in this way, including cracks spalls, pop-outs and delaminations. The growth of mold or mildew, and the decay of building materials can also be signs that there are moisture issues present within the substrate. Other problems to watch for include:
- Paint that shows signs of peeling or blistering
- Paint bubbles that retain water
- Signs of rust on the concrete facade
- Rotting wood
- Water that ponds in crawl spaces
Sounding the concrete by chain dragging, hammer, or other non-destructive test can uncover problem areas that can't be determined from a visual inspection.
How to Ensure Sound Substrates
Concrete evaluation and being equipped to handle concrete repairs are essential components of waterproofing projects. Following a visual inspection, the next steps include:
- Removing and preparing any identified deteriorated concrete
- Treating any existing corrosion on the rebar
- Treating cracks with an appropriate method.
For any larger cracks, 1/16" or wider, it's often a good idea to slightly expand the opening in the form of a V-shaped groove typically ¼" x ¼" . This makes the application of patching materials easier to complete. After unsound concrete is removed, use specific materials (grout,mortar or other repair materials) to complete this part of the project.
Once the concrete substrate is properly repaired, the waterproofing can then be installed. It is important to consult with the waterproofing manufacturer to ensure the concrete repair and waterproofing materials are compatible.
When applied to concrete substrates, waterproofing addresses the challenge of protecting this from water intrusion. The goal is reducing, or even eliminating, the threat of leaks and cracks to a concrete structure.
Durability and Structural Integrity
Properly prepared substrates are a big factor in prolonging the life of a building structure. This also includes repairing unsound or deteriorated substrates. Preparation can also protect against unwanted repairs in the future and/or the need for expensive new installation over time.
With a sound substrate in place, the application of appropriate waterproofing materials helps establish a protective obstacle against moisture, leaks and other related issues. This in turn contributes to the building's structural integrity. Commercial customers happy with the work of their waterproofing contractor are more likely to offer repeat business and refer the contractor to others.